Ultrafast ICCD Cameras Enable Three-Pulse Ballistic Imaging Technique
Overview
Although the use of sprays for industrial processes such as material deposition, cutting, and mixing is widespread, the design and testing of most spray devices is still predominantly phenomenological, owing not only to limitations in computing power but to gaps in the fundamental understanding of the multiphase fluid phenomena that drive spray breakup and morphology 1,2. One key to developing a first-principles understanding of sprays, therefore, is to devise methods for making measurements in turbid spray regions, particularly measurements that can offer insight into fluid motion and the forces active in spray mixing.1
Recently, researchers at Chalmers University of Technology in Sweden demonstrated a three-pulse configuration for time-gated ballistic imaging (BI) applied to a turbulent, steady spray; this technique, which utilizes a pair of ultrafast scientific ICCD cameras, permits the acquisition of time-correlated image data.1
The researchers report that the new approach images the liquid-gas interface of a spray, where shear forces and turbulence instabilities act to break the liquid apart. Region-matching analysis is subsequently applied to the time-correlated image data so as to compute the velocity and acceleration of resolved fluid structures.1
This application note will outline some of the novel work that has been performed by the group, which is led by Dr. Mark Linne, Professor of Applied Mechanics in the Combustion Division at Chalmers.
Experimental Setup
The Chalmers University experimental setup (shown in Figure 1) uses intense, ultrafast light pulses and specialized detection technologies to separate high-quality imaging light from diffusely scattered background light. The region of interest is illuminated with a series of coherent ultrafast pulses generated from a single oscillator that seeds three matched regenerative amplifiers 1.
ballistic imaging (M = mirror,P = polarizer, BS = beam splitter, BD = beam dump,
ICCD = intensified CCDcamera). Source light fromthree amplifiers is combined to
provide a high-energy train of three ultrafast pulses. Each source pulse is split into
imaging and switching paths to drivea Kerr-effect shutter and generate one ballistic
image.1 Diagramscourtesy of Prof. Dr. Mark Linne,ChalmersUniversity (Gothenburg,
Sweden). First published in D.Sedarsky,M. Rahm, and M. Linne, "Visualization of
acceleration in multiphasefluid interactions,"Opt. Lett. 41, 1404-1407 (2016).
Final collection of the high-quality imaging light from each source pulse is effected by dividing the optical signal exiting the Kerr gate into two detection paths. The images are acquired by two Princeton Instruments PI-MAX®4 scientific ICCD cameras equipped with intensifiers fiberoptically bonded to interline-transfer CCDs. The gain response of the intensifiers can
be gated to 5 ns and, using the interline-transfer sensors' masked storage areas in concert with specialized PI-MAX4 readout modes, each of the two cameras can generate a pair of images separated by as little as 450 ns. Thus, each individual PI-MAX4 can be set to capture consecutive image pulses (i.e., two images per camera). With this arrangement, each pulse train yields three time-correlated images of the spray.1
Data & Results
The Chalmers University steady-spray rig was employed to set up a controlled test case for measuring fluid velocity and acceleration in a turbid environment. Image-triplets of a water spray (Pinj = 19 bar) exiting a plain-orifice nozzle (L/d = 25) were acquired for dynamic ballistic imaging analysis. Figure 2 shows one of these image-triplets.1
the (6 mm dia.) nozzle. The view includes thespray periphery and the flowis from top to bottom
(flow rate ~60 lpm). Images I1, I2, and I3 show the same 8.6 mm field-of-view at 10 μsintervals
.1 Images courtesy of Prof. Dr. Mark Linne,Chalmers University (Gothenburg, Sweden). First published in
D. Sedarsky, M. Rahm, andM. Linne, "Visualization of acceleration in multiphase fluid interactions,
" Opt. Lett. 41, 1404-1407 (2016).
The primary objective of the Chalmers University three-pulse BI system is to enable the acquisition of spatially resolved time-series data that can be analyzed to track motion and changes in the imaged structure. Consecutive images in the series are compared and velocity vectors are computed for each time-step by selectively matching structure from targeted image regions. By computing coordinated sets of velocity vectors, the time-resolved displacement information acquired from multiple time-steps can be utilized to estimate higher order motion components.1
The velocity results for the spray imaged with the three-pulse BI system indicated large streamwise motion with small variations in the radial direction. The acceleration results indicated that the liquid structures were subjected to acceleration in the positive radial direction, and retardation in the streamwise direction. These results are indicative of both turbulence and shear forces affecting the breakup of the liquid jet.1
For a more detailed description of the experimental setup as well as an in-depth discussion of the results and their derivation, please refer to D. Sedarsky, M. Rahm, and M. Linne, "Visualization of acceleration in multiphase fluid interactions," Opt. Lett. 41, 1404-1407 (2016). Related investigations being conducted at Chalmers University of Technology include the use of a short-pulse, time-gated, backscattering setup designed to provide information on the spray-formation region of atomizing sprays.3
New ICCD Camera Technologies
Thanks to innovative picosecond gating technology developed by Princeton Instruments, the PI-MAX4 scientific ICCD camera platform (see Figure 3) is now even faster. This exclusive gating technology, which fully leverages the performance advantages of Princeton Instruments' state-of-the-art electronics and intensifier-to-CCD fiberoptic bonding, allows PI-MAX4:1024i ICCD cameras to gate conventional image intensifiers (which normally achieve ~2 to 3 ns gating) at <500 ps without compromising quantum efficiency. Princeton Instruments' built-in SuperSynchro programmable timing generator further enhances PI-MAX4 camera utility for high-precision, time-resolved applications.
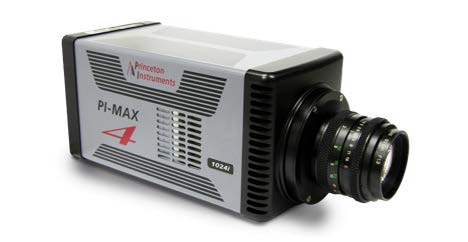
Figure 3. PI-MAX4:1024i ICCD cameras, which utilize
one of several Gen II orGen III filmless intensifiers
fiberoptically bonded to an interline-transfer CCD,
run at near-video rates (26 frames per second).
Another addition to the PI-MAX4 series, the PI-MAX4:2048f, provides four times the imaging area and resolution of any other scientific ICCD camera currently available on the market. This large-format camera, which uses a 2k x 2k CCD fiberoptically coupled to one of several 25 mm diameter Gen II or Gen III filmless intensifiers, offers built-in SuperSynchro, high frame rates (6 MHz / 16-bit digitization), and a 1 MHz sustained gating repetition rate.
Complete control over all PI-MAX4:1024i and PI-MAX4:2048f hardware features is simple with the latest version of Princeton Instruments' 64-bit LightField® data acquisition software, available as an option. Precision control of intensifier gate widths and delays, as well as a host of novel functions for easy capture and export of imaging data, are provided via the exceptionally intuitive LightField user interface.
References
- D. Sedarsky, M. Rahm, and M. Linne, "Visualization of acceleration in multiphase fluid interactions," Opt. Lett. 41, 1404-1407 (2016). [doi: 10.1364/OL.41.001404]
- T.D. Fansler and S.E. Parrish, "Spray measurement technology: a review," Meas. Sci. Technol. 26, 012002 (2015).
- M. Rahm, Z. Falgout, D. Sedarsky, and M. Linne, "Optical sectioning for measurements in transient sprays," Opt. Express 24, 4610-4621 (2016). [doi: 10.1364/OE.24.004610]